Even on items like luxury yachts and hi-tech aeroplane wings, the finishing touches in manufacturing are still done by highly skilled professionals using hand and eye. However, this is not a perfect system, and mistakes can lead to costly repairs or even completely unusable products. Now, a new project called FLASH-COMP is developing a system that uses artificial intelligence to ensure flawless manufacturing, right first time.
FLASH-COMP is a Horizon Europe project that is developing a fast and reliable quality control solution that uses artificial intelligence to help identify and remove defects during composite manufacturing processes. This zero-defect manufacturing approach will help reduce waste by more than 30% and help Europe’s planned transition towards climate neutrality
Reducing waste from composite manufacturing
The reduction of manufacturing waste is a key part of Europe’s planned transition towards climate neutrality. Composite materials represent an excellent target for reducing waste as they play an important role in several of the EU’s strategic manufacturing sectors, including energy, aerospace, naval and automotives.
Liquid resin infusion (LRI) is one of the most widely used composite manufacturing processes, accounting for about 33% of composite parts produced in Europe. It is used especially in the production of large parts such as wind turbine blades, airplane parts and ship decks.
Despite the high value of the parts produced using this process, both the material processing and quality control are largely done manually at the end of the manufacturing process, after which the parts are repaired or, if defects are too severe, discarded.

The traditional LRI manufacturing process. In an ideal world, once the resin is cured, finished, and checked, a final product is delivered, but problems may occur along this process.
To overcome the lack of automated in-line control and to guarantee that defects that arise during the process are not propagated to the final product, LRI manufacturing processes use far more raw materials than are needed for the final product, resulting in an excessive amount of waste.
In this context, controlling and reducing the generation of defects by adopting “first-time-right” manufacturing strategies based on novel in-line inspection and monitoring and advanced control strategies – known as a zero-defect manufacturing approach – is of high interest in LRI-based manufacturing processes, as it would allow the amount of material used to be optimised, reduce the reworking time, and reduce the number of fully rejected parts. It is estimated that a reduction of waste of more than 30 % can be achieved via such an approach.
FLASH-COMP: Composite manufacturing, right first time
FLASH-COMP is a Horizon Europe project that started in October 2022. Coordinated by Lortek in Spain, it is developing a fast and reliable quality control solution capable of identifying defects during LRI and, consequently, to determine in-situ corrective actions that can be implemented. This will help the push towards a zero-defects LRI manufacturing process, significantly reducing the generation of waste.
FLASH-COMP will employ novel, fast and accurate inspection and monitoring techniques within the most critical manufacturing stages – preforming and infusion – to retrieve key process parameters. This data will feed an AI-based tool capable of estimating the generation of defects and, in consequence, determining if and what kind of corrective actions should be adopted within the pre-forming and resin infusion operations.
Instructions will be linked to a real-time decision support system which will allow workers to take instant and precise corrective actions, paving the way towards “right-first-time” manufacturing. The smart knowledge will be fed from interoperable and sovereign data sharing between sites and factories. In this way, the composite sector will take advantage of the latest technological innovations to digitalise manufacturing processes towards a more sustainable and competitive composite industry.
How LRI is done at the moment
In traditional LRI processes, both material processing and quality control are largely done manually, with the quality of the final product being almost totally determined by an experienced operator. In most cases several reworking actions are needed during the process as well as repairs needed to the final product. In some cases, repair is not possible and the whole part is discarded. These activities are complex and account for around 30 per cent of the total production time, which makes the whole process highly inefficient.
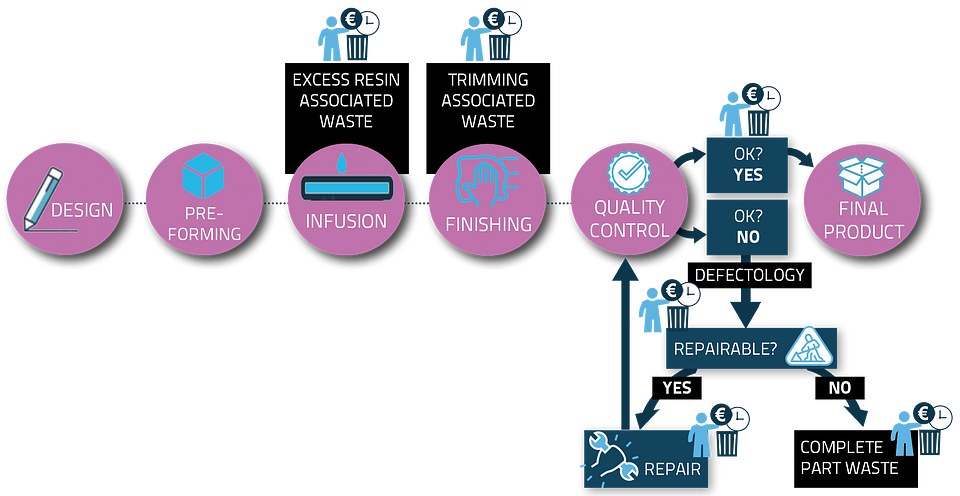
The FLASH-COMP approach
FLASH-COMP will use novel, fast and accurate inspection and monitoring techniques (FLASH-IM) within the most critical manufacturing stages of LRI, pre-forming and infusion, to retrieve key process parameters. This data will feed an AI-based defect severity estimation tool (FLASH-DSET), capable of estimating the generation of defects and, consequently, determining if and what kind of corrective actions should be taken at the pre-forming and resin infusion stage of operations. Instructions will be linked to a real-time feedforward and feedback (FF/FB) control strategy decision support system (FLASH-DSS) which will allow workers to take instant and precise corrective actions, paving the way towards ‘first-time-right’ manufacturing with zero-defects and zero-waste.
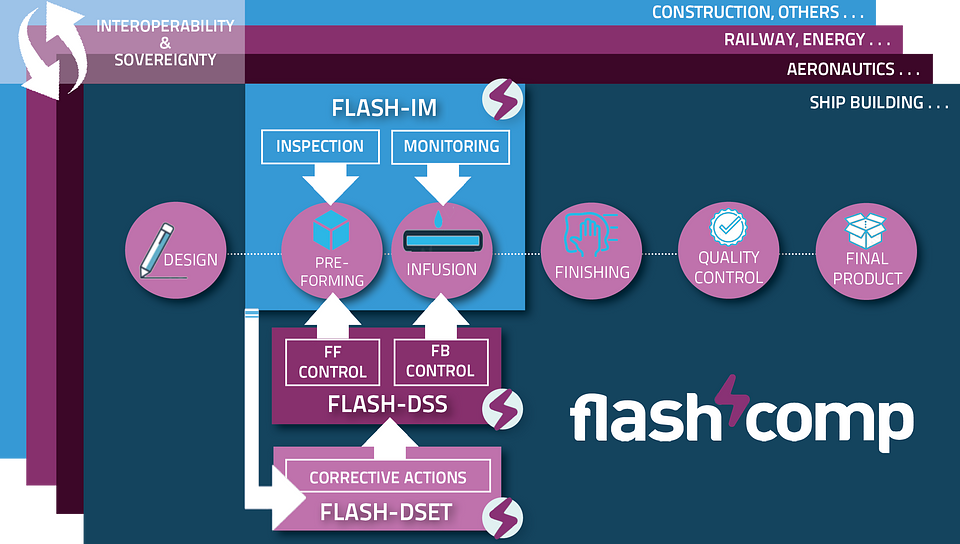
The FLASH-COMP pilot sites
The industrial feasibility of the FLASH-COMP solutions will be demonstrated and validated in two industrially relevant environments – shipbuilding and aviation – which cover different materials, part sizes, and monitoring and inspection challenges. An overall performance assessment will be carried out for each use-case to validate the greening capacity of FLASH-COMP solutions when implemented in industrial setups.
Azimut Yachts is an Italian yacht-manufacturing company based in Viareggio, Italy. The composite structures such as boat hulls that they produce for these yachts can be anywhere between 14-50 metres in length.
Israel Aerospace Industries (IAI) is Israel’s major aerospace and aviation manufacturer, producing aerial and astronautic systems for both military and civilian usage. IAI uses composite manufacturing to produce 72 wings per year.
What is the potential impact of the FLASH-COMP approach?
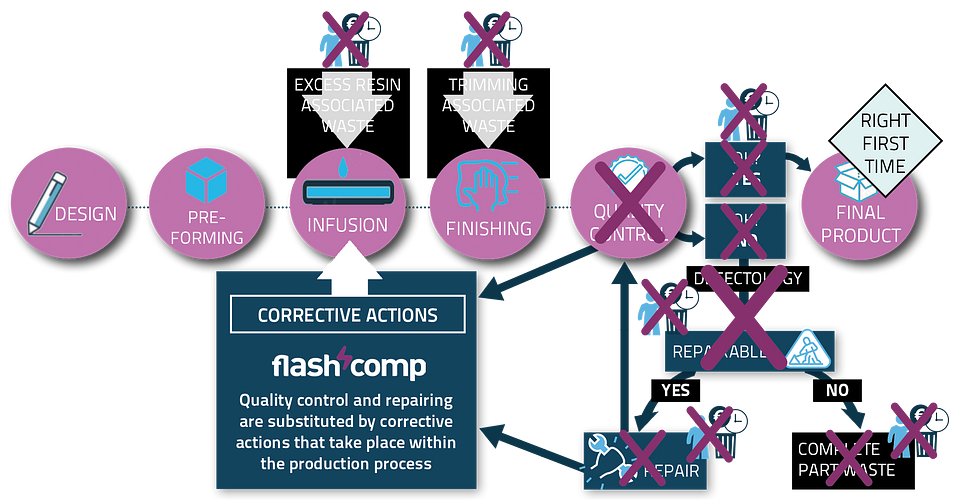
FLASH-COMP technology will reduce the amount of liquid resin used in the infusion process as well as reducing the amount of trimming required at the finishing stage. Meanwhile, with corrective actions taking place in line during production, the process of detecting defects and then repairing or discarding them will be removed from the quality control phase and the final product will be right first time.
It is estimated that a reduction of waste of more than 30 per cent can be achieved in this sector.
The human aspect of FLASH-COMP
One clear message from the FLASH-COMP project is that the solutions are not designed to replace people – they are designed to help people do their jobs more effectively.
FLASH-COMP is creating a decision support tool that will help workers to control the manufacturing process by either intervening directly or providing suggestions on how to proceed to guarantee the correct progress of the process. It will therefore be essential to put proper consideration into how this interaction between the decision support tool and the person involved works, to ensure that the FLASH-COMP solution is both accepted and valued by those who use it.
FLASH-COMP will integrate the needs and requirements of the users in the technical development of the FLASH-COMP solution, and use their suggestions about how to make the solutions more user-friendly and useful. It will also look to understand the impact of the new solution on the current work environment, identifying learning objectives to help current and future workers cope with the technological, process and cultural change that may come with the new solution.
Knowledge and methodologies from social sciences and humanities (SSH) will play a key role in this aspect of the FLASH-COMP project, with the aim of involving the end-users and workers from the beginning to shape the solution and to properly consider the learning competencies required to assure an effective integration of the FLASH-COMP solution.Several interviews with end users will take place at the beginning of the project, as well as observations of the different tasks they perform daily. Through an iterative process, the user’s perception of the technologies will be assessed and considered as the development of the solution progresses. This will be done through focus groups that include participants from a wide range of staff positions, from plant operators to management.
For more information on the FLASH-COMP project, visit the website or email harry@insightm.co.uk